Workplace asset inventory
Measuremen carries out an workplace asset inventory to provide you with a clear and workable list of inventory elements that you have in use. During the inventory, the information is collected and stored in an Excel file, in a format and layout that suits you best. An example Excel file is available to give you an idea of the result of the inventory. If possible, the file will be made suitable to be imported into, for example, your Facility Management Information System (FMIS).
Approach
Our approach to the WAI is thorough and contains interim quality controls. Measuremen makes an inventory of all available storage units and IT equipment required based on the discussion so far. This includes in particular the desks, IT resources, storage cabinets etc.
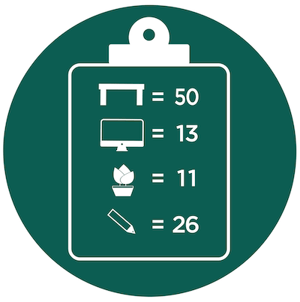
- Building / location
- Floor
- Zone or room number
- Element type
- Type
- Brand
- Model
- Colour
- Dimensions
- Complete / incomplete
- Comments
- Photo
- Barcode label + registration of code
- Photo
- Comments
- Complete / incomplete
- Dimensions
- Colour
- Model
- Brand
- Type
- Element type
- Zone or room number
- Floor
Other - records per element to be agreed during briefing to a maximum of 4 additional recordings per item (9 recordings in total)
Measuremen explicitly excludes the obligation to value the inventory.
The associated value and technical service life per element can, at a later date, be added to the prepared inventory file at an additional cost.
The implementation of the inventory and delivery of the data consists of the following components:
1. Preparation in preparation phase
During the preparation and preparation phase, the type of elements are determined in consultation with the client. Agreements will also be made about the desired format and the layout of the inventory file. The required forms and our database will be prepared by us, after which the order of the locations can be determined. In addition, the observers are recruited and screened.
2. Assessment
The inventories are performed through the pre-set catalog and works through a secure browser that our database owns. This makes the inventory independent of systems and processes on every mobile device. If necessary, the inventory can be carried out on hardcopy if circumstances so require.
3. Data quality
Both during and after the inventory, the data is extensively checked by our project coordinator. First a check is made whether everything is filled in. Inputs of answers that are considered striking are then checked extra.
4. Lead time
Based on previously implemented projects, we expect to register around 1,000 elements per day with a team of 2 observers. The total lead time of the project, with an estimate of the scope, is estimated at 2 inventory days.
5. Delivery
The results of the inventories are delivered no later than 5 working days after the last inventory day in a workable Excel file.